Expert Recommendations on What is Porosity in Welding and How to Resolve It
Expert Recommendations on What is Porosity in Welding and How to Resolve It
Blog Article
Porosity in Welding: Identifying Common Issues and Implementing Finest Practices for Avoidance
Porosity in welding is a prevalent issue that commonly goes undetected till it creates significant problems with the integrity of welds. In this discussion, we will certainly discover the key variables contributing to porosity development, examine its detrimental effects on weld performance, and review the finest techniques that can be adopted to lessen porosity incident in welding procedures.
Usual Sources Of Porosity
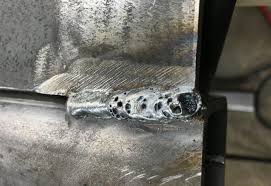
Utilizing unclean or wet filler materials can present pollutants right into the weld, contributing to porosity problems. To minimize these typical causes of porosity, comprehensive cleansing of base metals, proper securing gas choice, and adherence to optimal welding criteria are vital methods in achieving high-grade, porosity-free welds.
Effect of Porosity on Weld Quality

The presence of porosity in welding can substantially endanger the architectural integrity and mechanical residential properties of bonded joints. Porosity creates spaces within the weld steel, weakening its overall stamina and load-bearing ability.
Welds with high porosity degrees often tend to display lower impact strength and reduced ability to flaw plastically prior to fracturing. Porosity can hamper the weld's capability to efficiently transmit forces, leading to premature weld failing and prospective safety dangers in crucial frameworks.
Finest Practices for Porosity Prevention
To enhance the architectural honesty and high quality of bonded joints, what details actions can be implemented to minimize the incident of porosity throughout the welding process? Porosity prevention in welding is essential to make sure the honesty and stamina of the final weld. One reliable method appertains cleansing of the base metal, removing any kind of pollutants such as rust, oil, paint, or wetness that could bring about gas entrapment. Ensuring that the welding tools is in good problem, with clean consumables and ideal gas flow prices, can also dramatically minimize porosity. Additionally, keeping a stable arc and regulating the welding parameters, such as voltage, current, and travel rate, assists develop a consistent weld swimming pool that minimizes the danger of gas entrapment. Using the right welding technique for the particular product being welded, such as adjusting the welding angle and gun position, can further prevent porosity. Regular assessment of welds and immediate removal of any kind of problems recognized during the welding process are crucial methods to stop porosity and generate premium welds.
Value of Correct Welding Techniques
Carrying out correct welding visit homepage methods is vital in making certain the structural stability and high quality of bonded joints, developing upon the structure of effective porosity avoidance measures. Too much warmth can lead to enhanced porosity due to the entrapment of gases in the weld swimming pool. Additionally, making use of the ideal welding specifications, such as voltage, present, and travel rate, is crucial for attaining sound welds with very little porosity.
Furthermore, the selection of welding procedure, whether it be MIG, TIG, or stick welding, must line up with the particular demands of the job to ensure optimum outcomes. Correct cleansing and preparation of the base metal, as well as picking the ideal filler product, are also necessary elements of proficient welding strategies. By adhering to these finest techniques, welders can lessen the threat of porosity formation and create top quality, structurally audio welds.
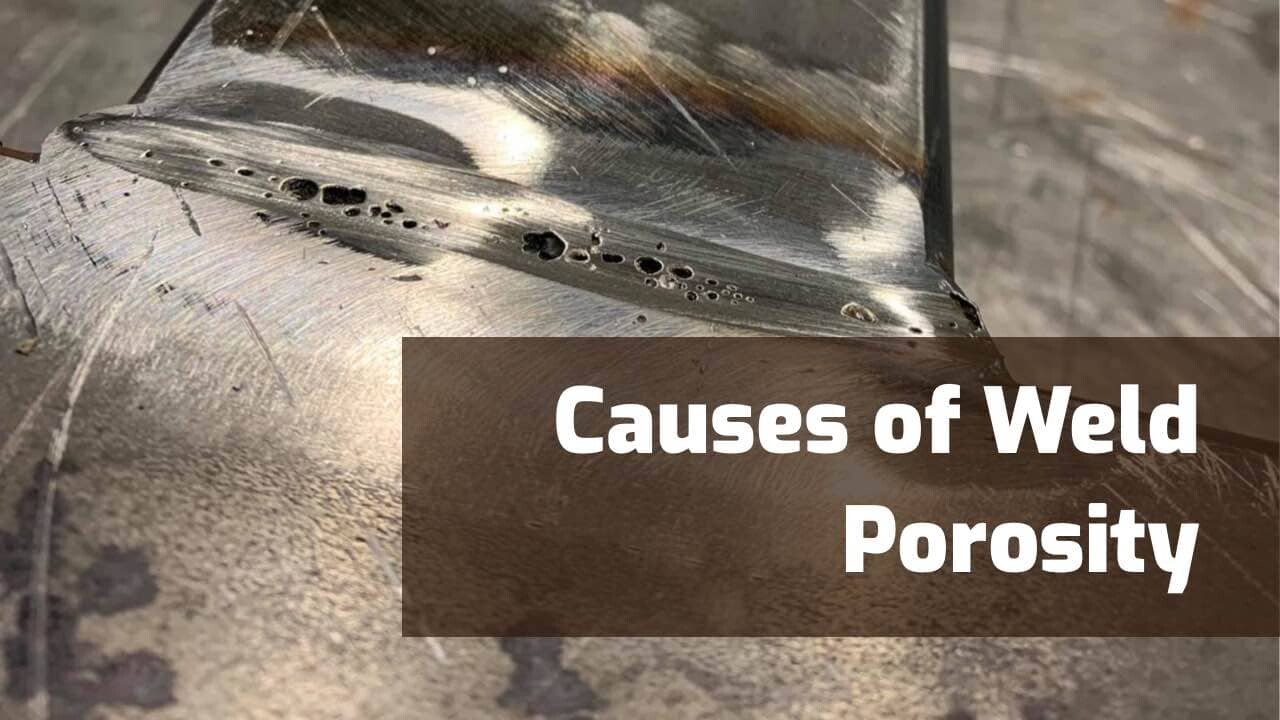
Testing and Quality Control Steps
Testing treatments are vital to discover and stop porosity in welding, making sure the toughness and longevity of the last item. Non-destructive screening approaches such as ultrasonic screening, radiographic testing, and aesthetic assessment are typically employed to recognize prospective flaws like porosity.
Post-weld assessments, on the various other hand, assess the last weld for any kind of problems, including porosity, and confirm that it satisfies specified requirements. Implementing a detailed high quality control strategy that includes extensive this testing treatments and evaluations is critical to decreasing porosity concerns and ensuring the general top quality of welded joints.
Final Thought
To conclude, porosity in welding can be click here now a typical problem that influences the quality of welds. By determining the typical causes of porosity and carrying out ideal methods for prevention, such as correct welding strategies and screening procedures, welders can make certain high top quality and trusted welds. It is vital to prioritize prevention approaches to lessen the incident of porosity and maintain the stability of welded frameworks.
Report this page